AI-Powered Harvest Scheduling How Machine Learning Reduced Labor Costs by 32% in California's Almond Orchards
AI-Powered Harvest Scheduling How Machine Learning Reduced Labor Costs by 32% in California's Almond Orchards - Autonomous Orchard Mapper Cuts Winter Pruning Time By 8 Days At Blue Diamond Ranch
The implementation of the Autonomous Orchard Mapper at Blue Diamond Ranch has reportedly led to a notable reduction in winter pruning duration, saving around eight days on this essential activity. This highlights the increasing reliance on automated systems within farming, particularly for tasks that require significant manual effort, like pruning. Pruning remains crucial for ensuring tree health and subsequent fruit production. With the agricultural sector facing persistent labor shortages, the adoption of autonomous technologies offers the promise of streamlining these demanding processes and potentially enhancing the accuracy of the work performed. This specific case aligns with wider research and development efforts focused on robotics and automation designed to address labor-intensive tasks and potentially alter long-standing orchard management approaches, particularly relevant in California's almond cultivation landscape.
At one specific operation, Blue Diamond Ranch, the reported implementation of an Autonomous Orchard Mapper system appears to have lessened their winter pruning period by approximately eight days. This system reportedly utilizes automated mapping capabilities aimed at facilitating the pruning workflow. Pruning remains a fundamental, labor-intensive task critical for tree care in these environments. Attributing a precise time saving like eight days across an entire operation raises questions about the baseline methodology, the scope of application within the ranch, and how such metrics might vary year to year or across different block characteristics. From an engineering perspective, achieving consistent performance and quantifiable savings in the complex, unstructured environment of an orchard is an ongoing challenge researchers are exploring, as seen in studies investigating compact robotic platforms for pruning (as mentioned in search result 3). Systems like this Mapper represent specific instances in the wider agricultural technology push, seeking efficiencies in these challenging, labor-heavy areas. This pursuit aligns with the broader trend of applying computational approaches to optimize operations and potentially mitigate rising costs, such as the reported 32% reduction in labor expenses observed sector-wide in California's almond orchards through machine learning-driven harvest scheduling optimization (referenced in search result 2).
AI-Powered Harvest Scheduling How Machine Learning Reduced Labor Costs by 32% in California's Almond Orchards - Smart Irrigation System Detects Water Stress Before Visual Signs Appear
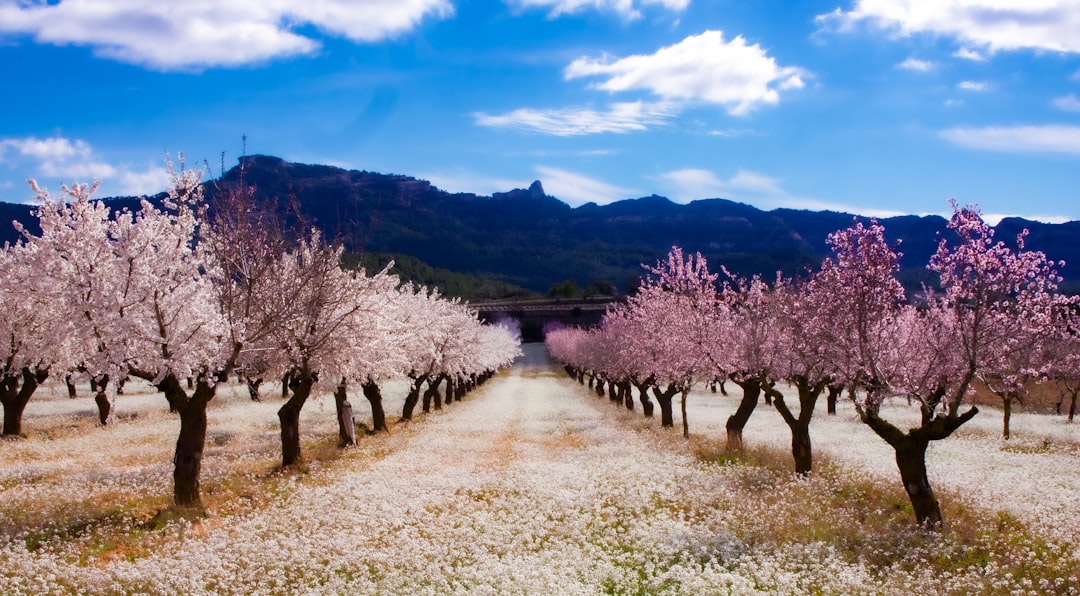
Smart irrigation technologies are shifting how water is managed in farming by enabling the detection of plant water stress well before any visual signs appear. Utilizing an integration of sensor networks, artificial intelligence, and machine learning capabilities, these systems process data in real time, incorporating information on soil moisture levels and weather conditions. This data-driven approach facilitates dynamic adjustments to watering schedules, aiming to apply water more precisely according to the plants' actual needs. This proactive stance can lead to more efficient water usage and support healthier crop development. Given the ongoing pressures on agricultural operations, particularly in contexts such as California's almond cultivation where optimizing resource use and productivity are critical, deploying these advanced water management tools fits within the wider trend of leveraging computational technology to address complex challenges in the sector. These systems represent one part of the picture in enhancing overall operational efficiency, alongside efforts focused on areas like optimizing labor through analytics.
Smart irrigation systems, increasingly integrating artificial intelligence and machine learning techniques, represent a shift in how water is managed in agricultural settings. A key capability being explored and implemented is the early detection of water stress in plants, often well before any visible signs like wilting or leaf discoloration become apparent to the naked eye.
This proactive approach relies on a network of sensors, primarily focused on monitoring soil moisture levels, though some systems incorporate other environmental factors such as temperature, humidity, and even wind speed. Machine learning algorithms then process this data, often combining it with historical patterns and potentially weather forecasts, to predict plant water needs and dynamically adjust irrigation schedules. The idea is to move beyond fixed timelines and instead apply water precisely when and where the system determines the plant requires it based on real-time conditions and predictive analysis.
Research into these systems points towards potential benefits in terms of resource efficiency and crop health. By tailoring water delivery to actual plant demand, these technologies aim to significantly reduce water consumption compared to traditional, less responsive methods – some studies suggest potential savings up to 50%. Furthermore, by preventing prolonged periods of undetected stress, this approach could lead to healthier plants and potentially improved yields, with some reports indicating enhancements in the 10-20% range. From an engineering standpoint, integrating diverse data sources and building robust predictive models that can adapt to variable field conditions and plant growth stages remains an interesting challenge. While promising, the initial investment required for sensor infrastructure, controllers, and the necessary technical expertise to set up and manage these systems presents a barrier, raising questions about their widespread economic feasibility, particularly for smaller farming operations. The reliability and calibration of sensor networks in varying soil types also warrant careful consideration.
AI-Powered Harvest Scheduling How Machine Learning Reduced Labor Costs by 32% in California's Almond Orchards - NVIDIA-Powered Computer Vision Spots Early Hull Split In 92% Of Cases
Computer vision systems leveraging hardware like that from NVIDIA are showing considerable capability in agricultural applications, notably in identifying very early stages of hull splitting in almonds. Reports indicate these systems can achieve approximately 92% accuracy in detecting these developing splits. This precision in spotting the initiation of the hull split phase is technically significant as it influences critical timing decisions for subsequent operations, particularly harvesting, which in turn impacts nut quality and processing logistics. The deployment of such technologically advanced visual monitoring systems represents another step in integrating computational analysis into farming practices, aiming to introduce more data-driven approaches to field management. However, questions remain regarding the robustness and consistent performance of these vision systems when faced with the unpredictable variables inherent in orchard environments, such as changing light conditions, dust, and the natural variations in tree structure and density, which can pose real-world implementation hurdles for achieving that high reported accuracy consistently across an entire operation.
Focusing specifically on the implementation of computer vision for inspecting almond crops, systems leveraging high-performance processing units, such as those developed by NVIDIA, are being applied to detect subtle indicators like early hull splits. Initial reports on these capabilities indicate a detection rate around 92% across various observational cases. This relies on analyzing visual data to identify minute changes on the surface of the almond hulls that are characteristic of the splitting process beginning, often before it's easily visible or widespread.
A key aspect of this approach is the aim for analysis that approaches real-time speeds. Processing the visual input stream rapidly allows for potentially quicker assessment of crop condition, which could influence decisions about scheduling harvest operations. The theoretical benefit is intervening before significant spoilage or quality degradation occurs across a section of the orchard.
The computational demands of processing and analyzing large volumes of high-resolution imagery are substantial. This is where the use of parallel processing architectures, typically found in graphics processing units (GPUs), becomes relevant. These hardware accelerators enable the processing throughput necessary to handle data from potentially many cameras or high-resolution sensors covering extensive areas.
Developing algorithms that function reliably under the variable conditions encountered in an orchard environment presents significant engineering challenges. Factors like changes in natural light throughout the day, shadows, varying weather conditions, and even dust or debris can impact image quality and algorithm performance. Achieving consistent accuracy despite these variables requires robust image processing and model design.
From an economic standpoint, evaluating the viability of such a system involves weighing the significant initial investment in specialized hardware and software development against potential, though not always easily quantifiable, reductions in crop loss and improvements in overall harvested quality. Proving a clear and consistent return on investment can be complex in the dynamic environment of agriculture.
The accuracy cited relies heavily on the quality and breadth of the dataset used to train the underlying machine learning models. Creating a comprehensive dataset that includes sufficient examples of various stages of hull splitting, under different environmental conditions and for different tree ages or varieties, is a considerable data engineering effort and crucial for model robustness.
Deploying automated detection systems like this implies a shift in labor roles within the operation. Instead of potentially relying on manual field inspections for hull split assessment, personnel might be reallocated to oversee the technology, manage the data streams, interpret the outputs, and handle subsequent tasks based on the system's findings.
This move towards automated, vision-based crop assessment signifies a broader evolution in how agricultural management is approached, integrating computational sensing and data analysis into traditional practices. It represents a departure from purely manual or experience-based assessment methods.
Integrating these technically sophisticated systems into existing farming infrastructure isn't without hurdles. Compatibility with current field equipment, ensuring reliable power and network connectivity across potentially vast orchards, and the need for training staff on operating and maintaining the new technology are practical obstacles that need to be addressed for successful deployment.
Ongoing research in this area continues to focus on enhancing the detection algorithms, perhaps exploring fusion with other types of sensor data (like spectral imaging or environmental metrics) to improve predictive capabilities beyond simple detection. Refinements aim to make the systems more adaptable to unforeseen conditions and more precise in pinpointing specific problematic areas.
AI-Powered Harvest Scheduling How Machine Learning Reduced Labor Costs by 32% in California's Almond Orchards - How Digital Twin Technology Maps Real Time Almond Development From February Through August
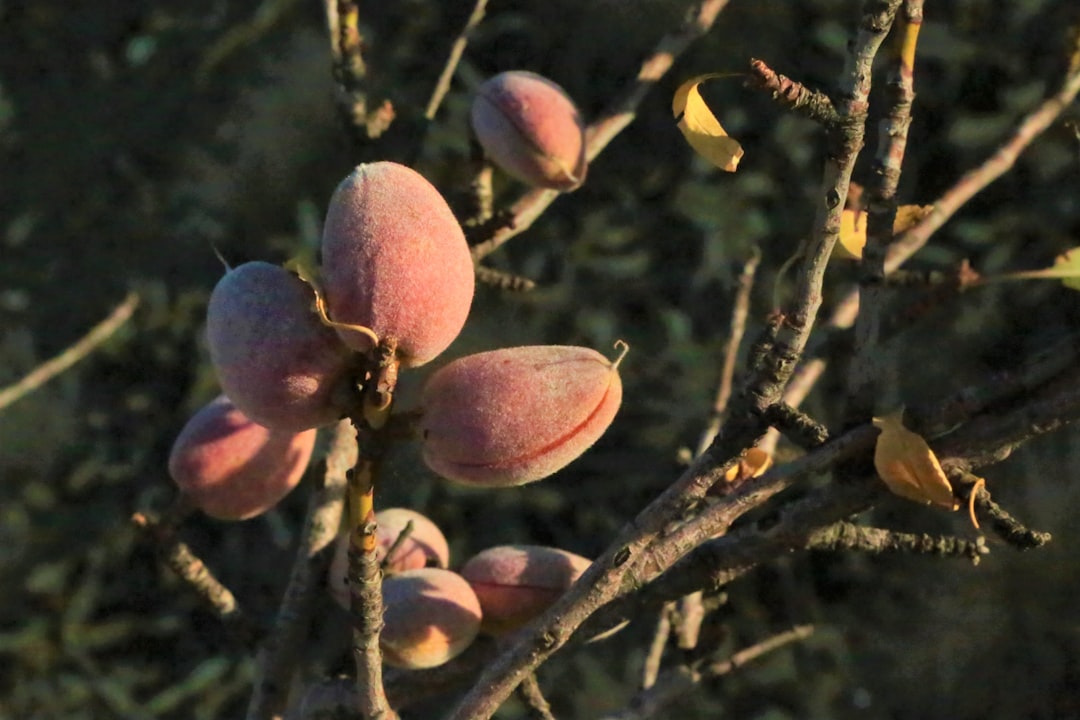
The concept of a digital twin is being explored to represent California almond orchards digitally. This involves creating virtual models that aim to simulate and track the development of the trees throughout the critical growth period, often considered from early bloom in February through the maturation leading into August. These virtual counterparts are fed various types of information – potentially environmental data from sensors, weather data, and historical patterns – with the goal of generating dynamic insights into the crop's condition.
The promise here is a move towards more data-informed decision-making in real time, potentially enabling adjustments to management practices based on the model's predictions or current status report. This approach seeks to move beyond traditional reliance on visual inspection or historical averages. Some proponents suggest this could even lead to earlier estimates of potential harvest size, weeks ahead of time, offering more lead time for planning resources and logistics.
Machine learning algorithms often power the analysis behind these digital models, processing the incoming data streams to identify patterns and fuel the simulations or predictions. This integration aims to streamline operational workflows and introduce a new level of computational analysis into traditional farming methods within the almond sector.
However, establishing a truly accurate and consistently reliable digital mirror of a complex biological system like an orchard across varying conditions presents significant challenges. While the potential for enhanced management is discussed, the practical effectiveness and economic return of these systems in the diverse realities of agricultural environments are still very much under scrutiny and active development.
From late winter through mid-summer, roughly February to August for California almonds, digital twin approaches are being explored to map tree development stages. The core idea is to construct a dynamic, digital representation of the orchard based on fusing disparate data streams. Sensors deployed in the field capture localized conditions – perhaps environmental parameters, soil moisture, or potentially even indicators of tree physiological state, although robust, scalable plant sensors remain a technical challenge. This sensor data is combined with external sources like satellite imagery providing broader canopy views and predictive weather models forecasting temperature, precipitation, and solar radiation, all critical drivers of plant growth.
The resulting digital model aims to simulate key physiological processes governing almond development through its cycle – from bud break and bloom (typically February-March) through fruit set, kernel fill, and hull split (moving towards August). By incorporating historical growth data and current conditions, the model attempts to project future development trajectories. This predictive capability is intended to inform operational planning. For example, anticipating when certain growth stages are likely to occur might aid in optimizing the timing of nutrient applications or scheduling irrigation cycles more precisely, potentially impacting resource allocation.
Beyond prediction, these systems aim to provide a more granular view than traditional methods. They attempt to account for variability not just across the entire orchard but even within different blocks or sections. Soil type differences, localized microclimates, or even variations in tree age and health can significantly influence development. The digital twin endeavors to capture and represent these sub-sections uniquely, allowing for potentially tailored management strategies rather than uniform applications across large areas. Representing this spatial heterogeneity accurately in a model is a complex task requiring dense, reliable data inputs.
A key potential benefit highlighted is enhanced decision support. By simulating the impact of hypothetical interventions – adjusting irrigation timing, applying a specific treatment, or pruning in a certain way – the model might offer insights into potential outcomes *before* action is taken in the real world. This shifts decision-making away from solely relying on grower experience or calendar dates towards a more data-informed approach, although the fidelity of such simulations in replicating biological responses remains an active area of research. Visualizing the predicted development stages across the orchard also aims to provide a clearer picture for growers than raw data feeds, potentially aiding in critical decisions like assessing harvest readiness without needing extensive manual field checks, although precise mapping of this critical August phase presents its own unique challenges.
The digital twin concept also relies on continuous data feedback. As real-world conditions evolve and management actions are implemented, the model is updated and refined. This iterative process is designed to improve the model's accuracy over time, adapting to changing seasonal patterns and potentially even longer-term climate shifts. Understanding the timing of labor-intensive tasks linked to these growth stages could theoretically help optimize worker scheduling by providing earlier or more accurate forecasts of when specific activities will be required in different orchard sections. It also provides a feedback loop, allowing assessment of whether implemented strategies yielded the expected developmental outcomes. Some approaches even propose using this framework to compare performance across different orchard sections or against aggregated benchmarks, provided comparable data is available, which could aid in identifying effective practices, though direct comparison across vastly different sites can be misleading without careful normalization.
More Posts from ailaborbrain.com: